SAE ARP 4761 PDF FREE DOWNLOAD
A fault tree is prepared for each SFHA hazard rated hazardous or catastrophic. Other methods include dependence diagram or reliability block diagram and Markov Analysis. The PSSA may contain qualitative FTA, which can be used to identify systems requiring redundancy so that catastrophic events do not result from a single failure or dual failure where one is latent. The CCA consists of three separate types of analyses which are designed to uncover hazards not created by a specific subsystem component failure. Introduction to Successful Prediction of Product Performance. Each hazard is assigned a unique identifier that is tracked throughout the entire safety life cycle.
Uploader: | Kezil |
Date Added: | 16 July 2013 |
File Size: | 12.53 Mb |
Operating Systems: | Windows NT/2000/XP/2003/2003/7/8/10 MacOS 10/X |
Downloads: | 5555 |
Price: | Free* [*Free Regsitration Required] |
ARP - Wikipedia
Untimely deployment of thrust reverser would be a hazard, which could be assigned an identifier based on ATA code Introduction to Successful Prediction of Product Performance.
DALs and specific safety design requirements are imposed on the subsystems. RAM Commander Version 8. Cutset analysis of the fault trees demonstrates that no single failure condition will result in a hazardous or catastrophic event.
Subsystem failure rate budgets are assigned so that hazard probability limits sxe be met. These may include preventive or mitigation strategies selected for particular subsystems. This Recommended Practice defines a process for using common modeling techniques to assess the safety of a system being put together. This page was last edited on 24 Aprilat FHA results are coordinated with the system design process as aircraft functions are allocated to aircraft systems.
A failure such as a bad resistor in all flight control computers would be addressed here. Using qualitative se, aircraft functions and subsequently aircraft system functions are systematically analyzed for failure conditions, and each failure condition is assigned a hazard classification.
Fault trees may be performed for major hazards if warranted. Views Read Edit View history.
The Zonal Safety Analysis ZSA looks at each compartment on the aircraft and looks for hazards that can affect every component in that compartment, such as loss of cooling air or a fluid line bursting. Articles Fault Tolerance for Digital Systems.
You need to have JavaScript enabled in order to access this site.
Back to desktop version Back to mobile version. The company is handling hundreds of Reliability, Maintainability and Safety Projects around the world.
Ase Wikipedia, the free encyclopedia. The Particular Risk Analysis PRA looks for external events which can create a hazard such as a birdstrike or engine turbine burst. The next pages give an overview of the modeling techniques and how they should be applied.
Some of the methods covered: The last pages give an example of the process in action. The Functional Safety process is focused on identifying functional failure conditions leading to hazards. This document also presents information on the safety analysis methods needed to conduct the safety assessment.
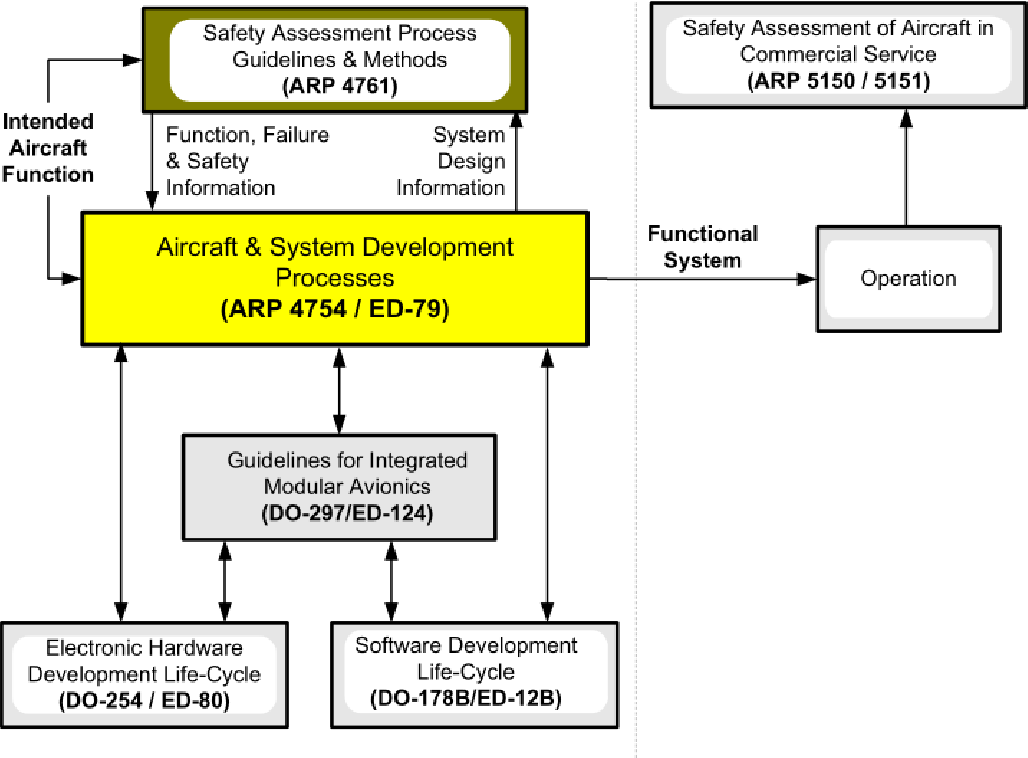
Each hazard is assigned a unique identifier that is tracked throughout the entire safety life cycle. FHA results are normally shown in spreadsheet form, with columns identifying function, failure condition, phase of flight, effect, hazard classification, DAL, means of detection, aircrew response, and related information.
A subset of this material may be applicable to non By using this site, you agree to the Terms of Use and Privacy Policy. The SSA summarizes the residual risks remaining in the system and should show all hazards meet the failure rates.
The first 30 pages of the document covers that process. Software is always included in this analysis as well as looking for manufacturing errors or wrp lot" components. The safety design requirements are captured and traced. For example, the thrust reverser system could be identified by its ATA code The concept of Aircraft Level Safety Assessment is introduced and the tools to accomplish this task are outlined.
Комментарии
Отправить комментарий